Laser welding technology has carved a niche for itself in the realm of metal joining, providing unparalleled precision and efficiency. Within this technological landscape, manual laser welding machines emerge as indispensable tools, offering a hands-on approach to achieving meticulous welds. In this article, we delve into the intricacies of manual laser welding machines, exploring their key components, advantages, and diverse applications across industries.
Brief Overview of Laser Welding Technology
Laser welding, a non-contact process utilizing laser beams to melt and join materials, has become synonymous with precision in the welding industry. The controlled application of energy through lasers minimizes distortion and heat-affected zones, setting it apart from traditional welding methods.
Significance of Manual Laser Welding Machines
While automated systems dominate certain manufacturing processes, the manual aspect brings a human touch to laser welding. Manual laser welding machines empower operators with control, allowing for intricate adjustments and adaptations that automated systems might struggle to achieve.
Key Components of Manual Laser Welding Machines
Laser Source and Beam Delivery System
Manual laser welding machines are equipped with either diode or fiber lasers. Diode lasers, efficient for shallow welds, find their place in precision applications. On the other hand, fiber lasers, known for their versatility and power, cater to a broader spectrum of welding requirements.
The efficiency of a manual laser welding machine relies heavily on precision optics. These optics facilitate the fine-tuning of the laser beam, ensuring it reaches the exact point of weld with utmost accuracy.
Control System and User Interface
The success of manual laser welding lies in the hands of the operator. Intuitive controls and user-friendly interfaces empower operators to navigate the welding process with precision, adjusting parameters on the fly for optimal results.
Real-time monitoring systems enable operators to observe the welding process closely. This, coupled with the ability to make instant adjustments, ensures that the manual welding machine adapts seamlessly to the evolving requirements of the task at hand.
Advantages of Manual Laser Welding
Submillimeter Welding Capability
Manual laser welding machines excel in achieving submillimeter welding precision. This level of accuracy is particularly crucial in industries where minute details can significantly impact the performance of the welded components.
Minimizing Heat-Affected Zones
By precisely controlling the laser beam, manual welding minimizes heat-affected zones. This feature is invaluable when working with materials sensitive to temperature changes, preserving the structural integrity of welded components.
Welding Diverse Materials with Ease
Manual laser welding machines exhibit a remarkable ability to weld diverse materials, including dissimilar metals. This versatility opens up a wide range of applications, from intricate jewelry design to heavy-duty industrial tasks.
Applications Across Industries
The adaptability of manual laser welding extends its reach across various industries, including automotive, aerospace, electronics, and medical. The capability to work with different materials positions it as a go-to solution for an array of welding needs.
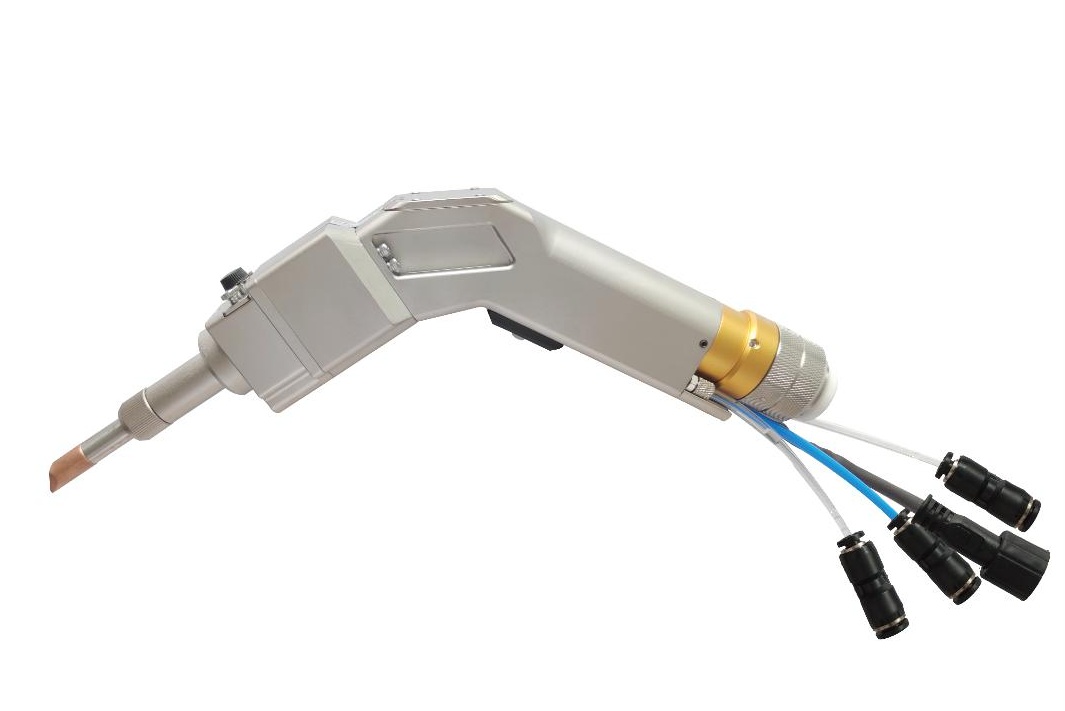
Customized laser metal welding machine for sale
Applications and Industries
Automotive Manufacturing
In the automotive industry, where different metals are often used in a single vehicle, manual laser welding machines play a crucial role in seamlessly joining dissimilar materials. This is essential for enhancing structural integrity and reducing overall weight.
Manual laser welding machines find applications beyond manufacturing. They are instrumental in repairing and modifying automotive components with precision, extending the lifespan of critical parts.
Aerospace and Defense
The aerospace industry's pursuit of lightweight materials for enhanced fuel efficiency and performance aligns perfectly with manual laser welding capabilities. The machines delicately weld lightweight materials critical for aircraft design.
Manual laser welding ensures the fabrication of critical components for aerospace and defense applications. Its precision is paramount in creating components that meet stringent safety and performance standards.
Conclusion
The manual laser welding machine stands at the forefront of welding technology. Its versatility, coupled with the ability to achieve submillimeter accuracy, makes it an indispensable tool across industries where precision and adaptability are non-negotiable. As manufacturing landscapes evolve, manual laser welding machines continue to shape the future of metal joining with their intricate capabilities and diverse applications.
Share This Post: